Temperature and pressure resistance to improve work efficiency F-class 1UEW enamelled self-adhesive coil industrial electronic medical
Product name: F-class 1UEW enamelled self-adhesive coil
Product name: F-class 1UEW enamelled self-adhesive coil
· Self-adhesive enameled wire (self-adhesive wire), also known as self-melting wire, has an additional layer of self-adhesive paint on the surface of the enameled wire.
· It is very difficult to manufacture the complex-shaped frameless coils used in early TVs and some micro motors with ordinary enameled wires. The manufacturing process of this type of armature coil is rather peculiar. First, a single winding must be processed and formed, and then each formed winding is formed into an armature winding. The single winding forming method used to be to apply adhesive on the outer surface of the enameled wire to fix it on the mold, and then bake and shape it. The motor winding forming process has achieved very good economic results. It is widely used in key components of electronic products such as coreless motors, self-adhesive coils, micro-motors, electronic transformers, sensors, and electronic components. The promotion of armature and transformer armature.
Bonding process:
The self-adhesive layer coated on the surface of the self-adhesive wire can produce adhesiveness through the action of high temperature or chemical solvents
High temperature/heat bonding:
All Elektrisola self-adhesive layers can be bonded by heating. The wire can be heated directly with hot air during the winding process, or the wound coil can be heated through an oven, or current can be applied to the coil after the winding is completed. The principle of all these methods is to heat the winding coil to a temperature slightly above the melting temperature of the self-adhesive layer, so that the self-adhesive layer melts and bonds the wires together. Air-through bonding has the advantage of not requiring a secondary bonding process after winding. This method is cost-effective and is mainly used for self-adhesive wires with dimensions smaller than 0.200mm. This method has become more popular over the past few years with the development of ultra-high temperature self-adhesive layer types.
Oven bonding:
Oven bonding is accomplished by heating the wound coil. The coil is still kept on the fixture or tooling during winding, and the entire coil is heated evenly in the oven at an appropriate temperature and sufficient time, and then cooled. The heating time depends on the size of the coil, usually 10 to 30 minutes. Disadvantages of oven bonding are longer self-bonding times, additional process steps, and potentially greater demands on the number of wire-wound tooling.
Electrobonding:
This is done by applying an electric current to the finished coil and generating heat through its resistance to achieve the proper bonding temperature. The voltage and time of energization depend on the size of the wire and the coil design and therefore need to be experimentally developed for each specific application. This method has the advantages of fast speed and uniform heat distribution. It is usually suitable for self-adhesive wire with wire diameter size greater than 0.200mm.
Solvent bonding:
Certain self-adhesive layers can be activated using specific solvents during the coil winding process. When winding, a solvent-soaked felt ("wet winding") is usually used to soften the self-adhesive layer. This process requires the use of a tooling to hold the coils in place, and the coils are bonded together after the solvent dries. The coil should then be heated in an oven for one cycle to evaporate residual solvent and complete the self-adhesive layer curing process for optimum bond strength. If there is any solvent remaining in the coil, it may cause the coil to fail after a long time.
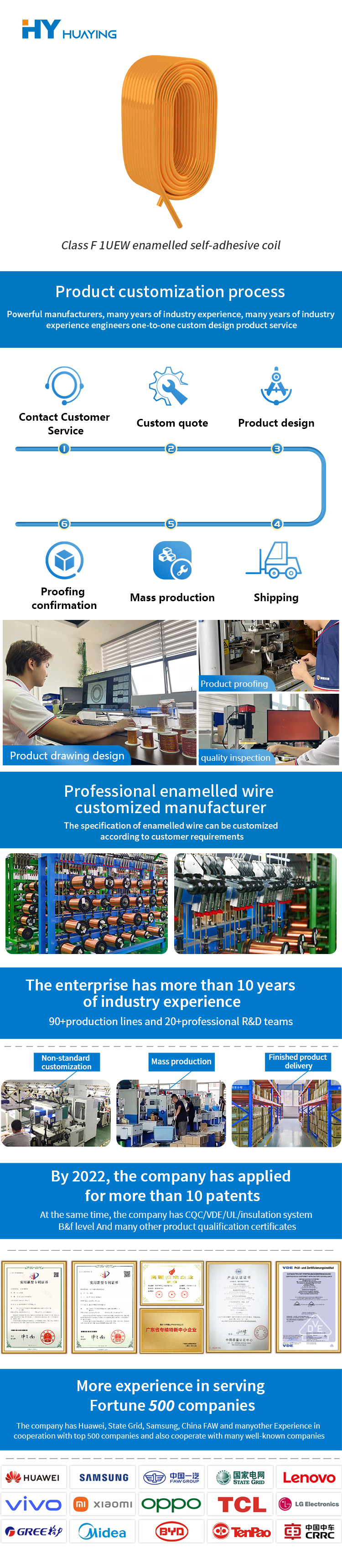